Harnessing Efficiency: The Potential of Quick Injection Molding
In the current fast-paced production landscape, the need for swift product development has often been more significant. Businesses across multiple industries are regularly seeking ways to optimize their production methods and launch their ideas to market in a shorter time. One method that has surfaced as a revolutionary advancement is fast injection molding. This pioneering approach not only speeds up the manufacturing process and also enhances effectiveness and lowers costs, establishing it a key component in the quest for quicker and more effective product creation.
Rapid injection molding offers a unique solution for companies looking to create premium plastic items in brief time frames. By employing state-of-the-art technologies and techniques, manufacturers can rapidly create prototypes and expand production without sacrificing precision or nuance. As companies strive to stay in the game, understanding the features of rapid injection molding becomes vital for unlocking effectiveness and enhancing productivity.
Overview of Rapid Molding Techniques
Rapid injection molding is a advanced manufacturing process that considerably reduces the time required to produce plastic parts for multiple industries. This method involves the use of state-of-the-art technologies and materials to optimize the molding process, allowing for speedier turnaround times without compromising quality. By leveraging rapid tooling and custom injection molding machines, manufacturers can create prototypes and production parts rapidly, addressing the growing need for speed in product development.
One of the primary advantages of rapid injection molding is its ability to accommodate design changes swiftly. In conventional injection molding, making alterations can be lengthy and expensive due to the need for new molds. However, with rapid injection molding, makers can alter their designs instantaneously, enabling them to enhance products and respond to market demands more efficiently. This adaptability not only reduces the product development cycle but also boosts overall competitiveness.
Furthermore, rapid injection molding is increasingly becoming an integral part of the prototyping phase for new products. It allows companies to create small batches of parts for trial and assessment, which can lead to valuable insights before launching mass production. The combination of speed, flexibility, and cost-effectiveness makes rapid injection molding a robust tool for streamlined product manufacturing, offering clear advantages for businesses aiming to innovate and thrive in their respective markets.
Benefits of Fast Inject Molding
Rapid injection molding offers substantial advantages in terms of velocity and efficiency for product production. One of the main advantages is the reduction in turnaround time. Traditional injection molding can take weeks or even years to create molds and finish parts, while quick injection molding can cut this time down to just days. This speed allows companies to keep pace with market demands and react swiftly to consumer needs, outpacing rivals.
In furthermore to quickness, rapid injection molding offers cost-effectiveness, especially for low to medium volume production. This method allows for the quick production of prototypes and small batches without the significant expenses associated with conventional molding. Producers can evaluate designs, collect feedback, and make changes swiftly, saving both time and money. This agility is crucial in the current fast-moving market where being able to quickly pivot or adapt designs can lead to improved sales and customer satisfaction.
Additionally, the versatility of rapid injection molding cannot be overlooked. It accommodates a wide range of substances and is appropriate for complex designs, allowing for innovative designs that might not be feasible with traditional methods. This flexibility enables businesses to explore new product concepts and enhance existing ones, ultimately leading to better product lines. By leveraging this technology, manufacturers can not only boost their output but also elevate the standard of their goods, supporting sustained growth.
Implementation and Examples
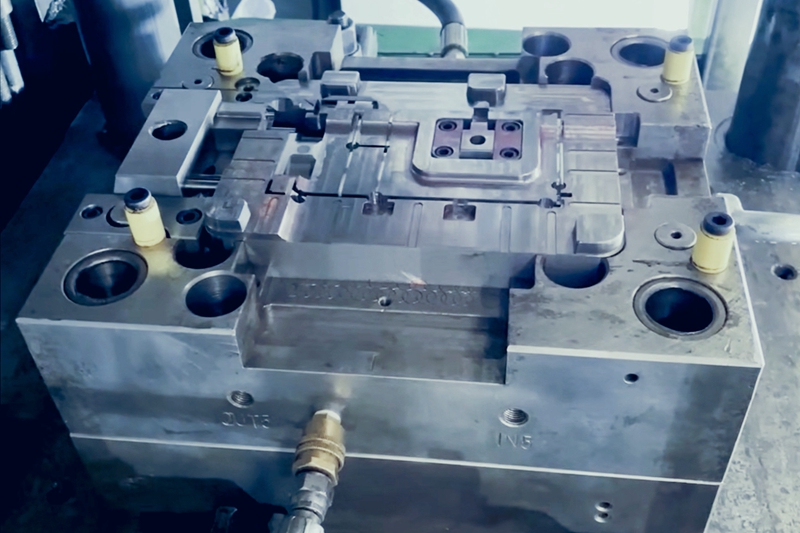
Swift injection molding is extensively applied across multiple industries, showcasing its flexibility and efficiency in different applications. In the vehicle sector, for example, manufacturers turn to rapid injection molding for the production of complex components such as dashboards and enclosures. The ability to quickly create and iterate designs allows for more efficient prototyping and testing, ultimately speeding up the time to market for recent vehicle models.
Another important application can be found in the tech industry. Companies often require high-precision parts for devices like smartphones and slate devices. Rapid injection molding satisfies this need by enabling the production of complex designs at a more affordable cost and with shortened lead times. A significant case study involved a prominent tech firm that cut the development cycle of a new product by 30 percent, thanks to the efficiency of rapid injection molding in creating prototype parts rapidly.
Additionally, the medical device industry has adopted rapid injection molding to produce extremely specialized components. For instance, a medical device company leveraged this technology to develop housings for testing equipment, enabling rapid iterations that meet stringent regulatory and performance standards. This approach also improved the speed of the manufacturing process but also enhanced the capability to tailor products according to specific patient needs.